Amorphous Plastic
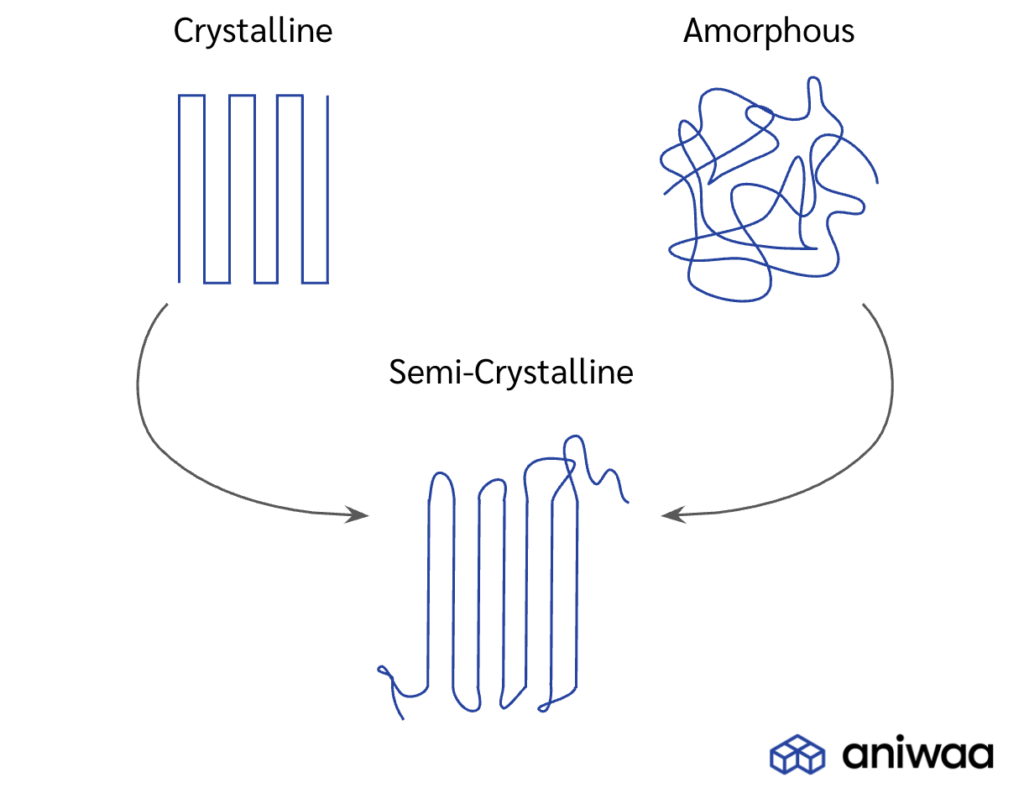
Amorphous plastics, also known as thermoplastics, are plastics that lack a specific crystalline structure. These plastics typically have a homogeneous, glass-like structure. When heated, they soften gradually, eventually melting into a viscous liquid. Some common examples of amorphous plastics include polystyrene, ABS (acrylonitrile-butadiene-styrene), and PET (polyethylene terephthalate).
In injection molding, amorphous plastics require consistent heat to achieve a uniform melt. Therefore, temperature control plays a crucial role in the injection molding process for amorphous plastics. Overheating or underheating the plastic can lead to inconsistencies in the melt, which can result in poor part quality or even product failure. Additionally, the cooling process is also important to ensure that the plastic solidifies uniformly and avoids warping or cracking.
Semi-Crystalline Plastic
Semi-crystalline plastics, on the other hand, have a more ordered molecular structure. This gives them a higher melting point and specific melting behavior. When heated, semicrystalline plastics exhibit a “two-step” melting process, where the crystalline portion melts at a higher temperature than the amorphous portion. Some common examples of semicrystalline plastics include polypropylene, nylon, and PEEK (polyetheretherketone).
In injection molding for semicrystalline plastics, melting temperature control becomes more critical. The two-step melting process means that the plastic must be heated to a specific temperature range to ensure uniform melting. If the plastic is overheated, the amorphous portion may begin to degrade, leading to quality issues. Additionally, cooling rate becomes more important, as the crystalline structure must solidify uniformly to avoid creating weak spots or stress points in the finished part.
Conclusion
Understanding how different plastic types melt is critical to ensuring quality in injection molding. Whether using amorphous or semicrystalline plastics, temperature control and cooling rate must be carefully monitored to achieve a uniform melt and avoid issues such as warping, cracking, and stress points. At the same time, manufacturers can use these materials’ unique properties to create parts with specific characteristics, such as rigidity, flexibility, or heat resistance. By understanding the differences between melting amorphous and semicrystalline plastics, manufacturers can optimize their injection molding process and create high-quality plastic injection molding parts.