Introduction
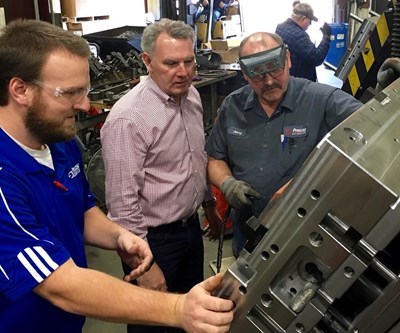
In today's competitive manufacturing industry, companies are constantly striving to improve their production processes and deliver high-quality products to their customers efficiently. Two critical aspects that play a significant role in achieving these objectives are tooling and molding. This blog aims to delve into the world of tooling and molding and shed light on their importance in the manufacturing process.
What is Tooling?
Tooling involves creating specialized tools and equipment required for the manufacturing of products. These tools can range from small handheld devices to large, complex machinery. The purpose of tooling is to shape, cut, form, or perform various operations on raw materials to achieve the desired product specifications. Tooling ensures precision, accuracy, and consistency while reducing the risk of errors during production.
Different types of tooling equipment, such as dies, molds, jigs, and fixtures, are used based on the specific manufacturing requirements. These tools are often designed with computer-aided design (CAD) software and manufactured using cutting-edge technologies. Precision tooling is crucial in industries such as automotive, aerospace, medical, and electronics, where even the slightest deviation can compromise the product's quality and performance.
What is Molding?
Molding, on the other hand, refers to the process of shaping and forming raw materials into the final product. It involves using a specially designed mold to create three-dimensional objects with a consistent shape and size. Molding techniques are widely employed to manufacture items like plastic parts, metal parts, glass products, and composite materials.
Injection molding is one of the most common methods used for creating plastic components. It involves injecting molten plastic material into a mold cavity, followed by cooling and solidification. This results in the creation of a detailed, finished product with minimal post-processing requirements. Injection molding is highly efficient, cost-effective, and allows for large-scale production.
Understanding the Relationship Between Tooling and Molding
Tooling and molding share an inseparable relationship in the manufacturing process. Tooling is essential for creating the molds used in molding, as well as any other tools needed for secondary operations such as trimming, cutting, or engraving. A well-designed mold improves the accuracy and efficiency of the molding process and ensures consistent part production.
Tooling also plays a crucial role in reducing downtime and increasing productivity. By having efficient tooling systems in place, manufacturers can minimize equipment maintenance and changeover times. This allows them to meet tight production deadlines and fulfill customer demands promptly.
Keywords: Tooling, Molding, Manufacturing Industry, Precision, Injection Molding, Relationships, Efficiency, Productivity.
Advantages of Tooling and Molding
1. Enhanced Efficiency: The integration of tooling and molding allows for a streamlined production process with fewer errors or defects. The consistent manufacturing that these processes offer significantly reduces waste and increases overall efficiency.
2. Cost Reduction: By employing tooling and molding techniques, manufacturers can produce products in large quantities, often at a lower cost per unit. The high level of automation in these processes reduces the need for manual labor, saving on operational expenses.
3. Design Flexibility: Tooling and molding techniques enable manufacturers to create complex and intricate designs, enabling better product functionality and aesthetics. With the advancement of technology, prototypes and new product iterations can be developed quickly and precisely.
4. Faster Time-to-Market: Tooling and molding processes speed up production cycles, allowing manufacturers to bring their products to market faster. The ability to produce large quantities in less time enhances competitiveness and helps secure market share.
Conclusion
As the manufacturing industry evolves, companies must embrace innovative techniques to maintain a competitive edge. Tooling and molding play a pivotal role in achieving operational efficiency, accuracy, speed, and cost-effectiveness. By leveraging advanced technologies in tooling design and molding processes, manufacturers can produce high-quality products that meet customer expectations. With the growing demand for customized products and faster time-to-market, tooling and molding remain vital components of the manufacturing industry's success.
Keywords: Tooling, Molding, Manufacturing Industry, Precision, Injection Molding, Relationships, Efficiency, Productivity, Cost Reduction, Design Flexibility, Time-to-Market.