1. Wall Thickness
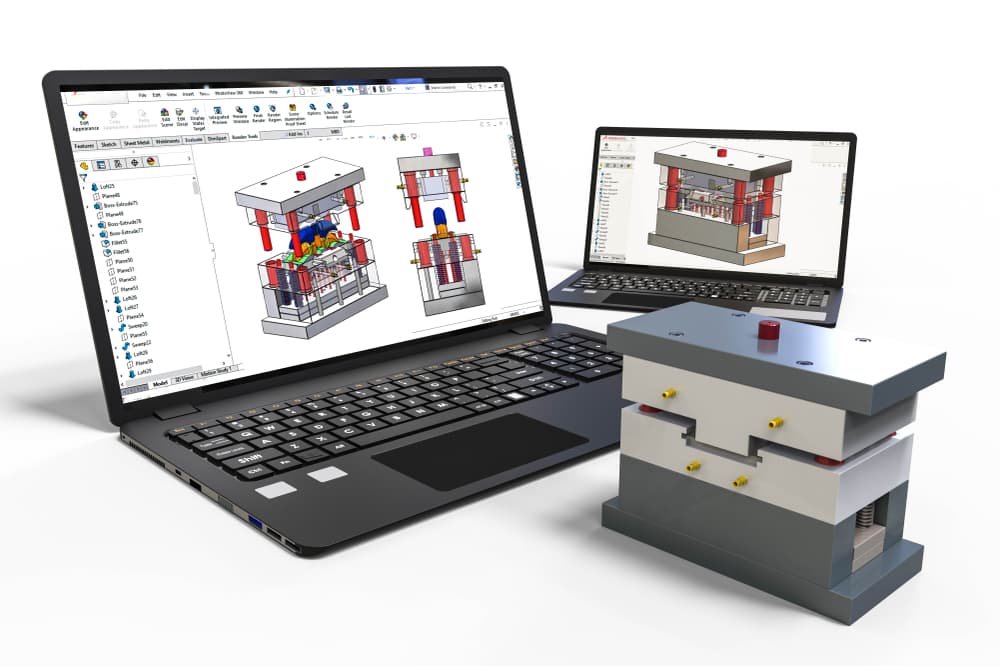
One of the most important aspects of designing injection-molded parts is to ensure that the wall thickness of the part is consistent. Variations in wall thickness can cause defects in the final product, such as warpage, shrinkage, and sink marks. Therefore, designers should aim to keep the wall thickness as even as possible.
2. Part Design
The part design must be optimized for injection molding. Designers should avoid sharp corners, undercuts, and thin walls that may cause manufacturing issues. The design should be simple and straightforward to allow for high-quality and cost-effective production.
3. Gate Design
The gate is the point where the molten plastic enters the mold cavity. Designers must choose the appropriate gate design depending on the part's geometry, material, and production volume. The gate's location and size can affect the part's quality, so the gate should be placed in an inconspicuous area, such as the part's backside.
4. Draft Angle
Draft angles are critical for enabling parts to be ejected from the mold cavity without being damaged. Draft angles should be incorporated into the design to avoid scratches, deformations, and other cosmetic defects. The angle should be at least 1° per side and could be more depending on the part's geometry and material.
5. Ribs and Bosses
Ribs and bosses are commonly used in injection-molded parts to add strength and rigidity. Designers should ensure that the ratio of rib thickness to part thickness is not greater than 60%, as this could cause sink marks and warpage. Bosses should be designed with sufficient draft to facilitate part ejection.
6. Material Selection
The selection of the material depends on the part's end-use application and requirements. The filling behavior, shrinkage, and warpage of the material can affect the quality of the final product. The material supplier should provide the necessary information for selecting the appropriate material.
7. Cooling Design
The cooling system is essential for controlling the temperature of the mold during the molding process. The cooling design should ensure that the temperature is uniform throughout the mold cavity. Uneven cooling can cause warpage, sink marks, and dimensional instability.
8. Venting
Venting allows trapped air and gas to be released from the mold cavity during the injection molding process. Venting is necessary to avoid defects such as air entrapment, burn marks, and jetting. The location and size of vents must be carefully considered during the design stage.
9. Ejection System
The ejection system is responsible for removing the molded part from the mold cavity when it cools and solidifies. The ejection system should be designed to facilitate easy and quick part removal, without damaging the part or mold. The ejection pins should be placed in areas that are inconspicuous and easy to repair.
10. Mold Maintenance
Proper mold maintenance is essential for ensuring the quality and longevity of the mold. Regular cleaning and maintenance can prevent defects such as contamination, flashing, and wear. A reliable injection tooling molding company should have a thorough maintenance schedule and a qualified team of technicians.
In conclusion, injection molding design requires careful consideration of several critical quality design considerations. Diverse factors such as the designed part, materials selection, part production volume, cooling system, and mold maintenance should be given due attention. To have high-quality injection-molded parts, teaming up with a reliable injection tooling molding company can make all the difference.